How can we help you today?
Solar cabling for commercial ground mount systems, Part 2, there's more!
DC solar cable, some more ground mount action!
We continue on from part 1 in this solar cable for a 1 MW ground mount system series. Parallel strings, voltage drop considerations and allowing for errors when calculating your runs are all examined.
Things to think about.What about voltage drop calculations? What percentage increase should I allow for bends? What about mistakes? Should we parallel the strings instead?
Recap from part 1
The assumptions:
- Using 400 watt panels
- 1690 mm long and 1046 mm wide
- Configured in Portrait
- 2 x tiers
In addition looking at:
- 20 x panels per string
- Gap between tiers is 25 mm
- Gap between panels is 25 mm
- No parallel strings
- Inverters all on back of last row
- All DC runs from middle of the row to middle of last row
Panel layout
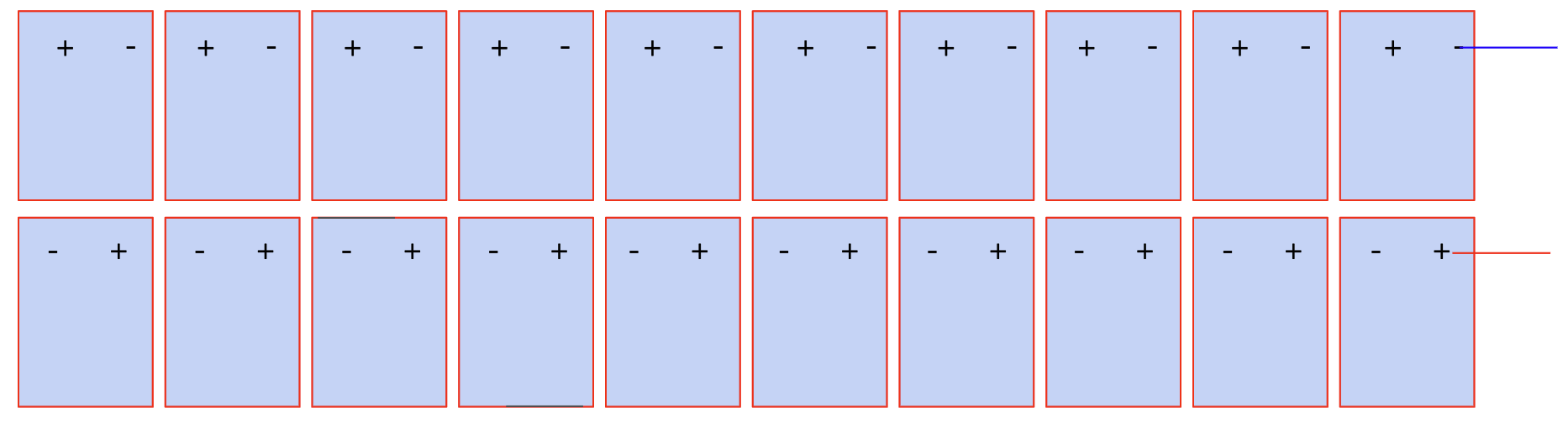
Per row there are 8 x strings of 20 x 400 watt panels per string so row length is approximately 85 metres wide.
There are 20 rows, total distance, North South with spacing is 142 metres which includes the 4 metre North and 4 metre South perimeter roads.
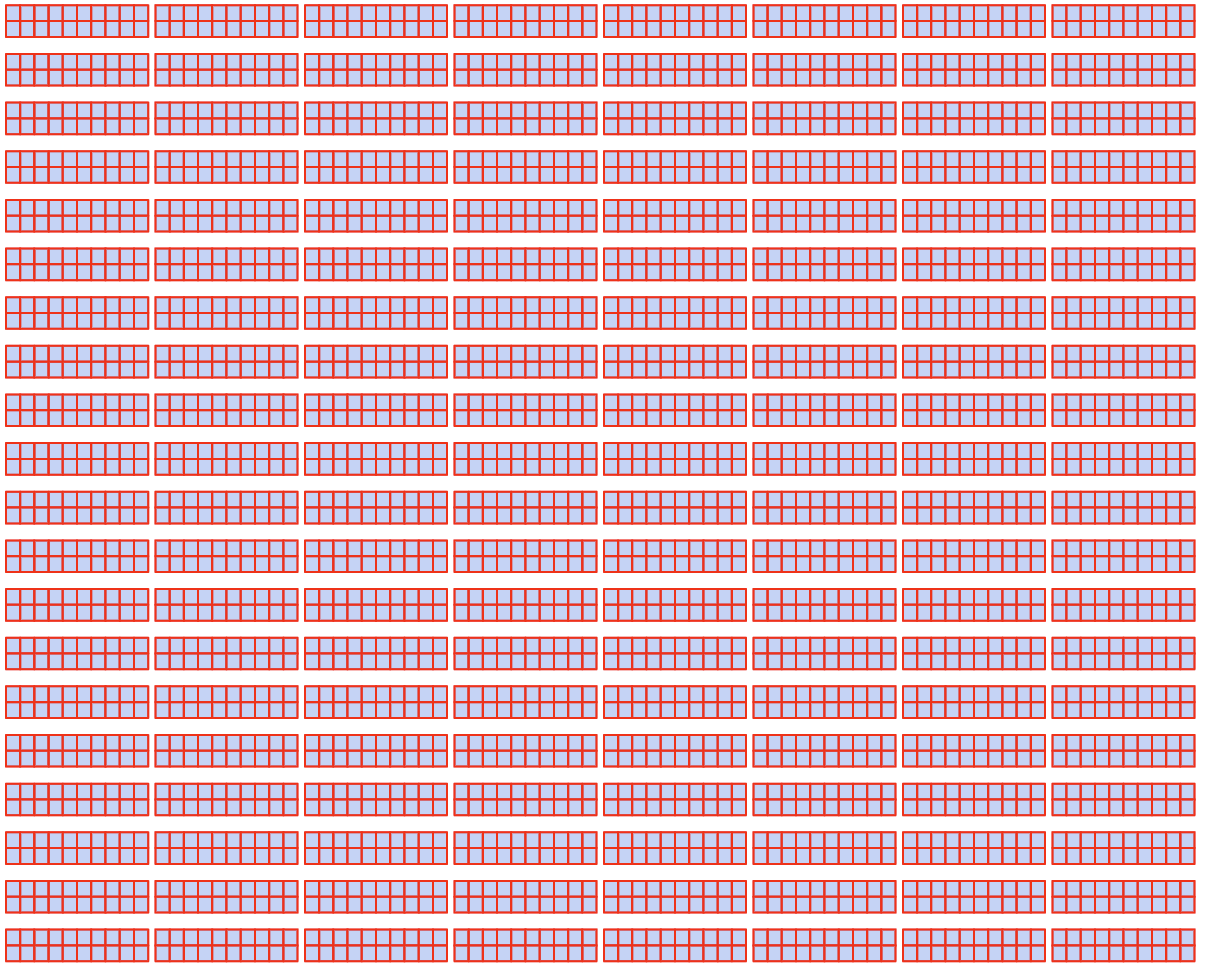
Distance from row 1 to row 20 is approximately 133 metres ( excluding perimeter access roads North South, 4 metres each)
- There is 160 strings, no parallel strings
- A lot of cable, in fact over 27,000 metres
- Each row requires 256 metres of DC cable
- And then there is the runs to the inverter station which is located behind row 20
Things to think about
We have all these cable runs resulting in more than 27,000 metres of cable in all and there are some questions to ask:
- What about voltage drop calculations?
- What percentage increase should I allow for bends?
- What about mistakes?
- Should we parallel the strings instead?
What about voltage drop calculations?
We need to maintain less than 3% on the DC volt drop side according to CEC recommendations.
- Are we using 4, 6 or 10 mm2 cable or a combination of all
- There are some really long runs to the inverter, row 1
- And also some really short runs
- All of this needs to be taken into consideration
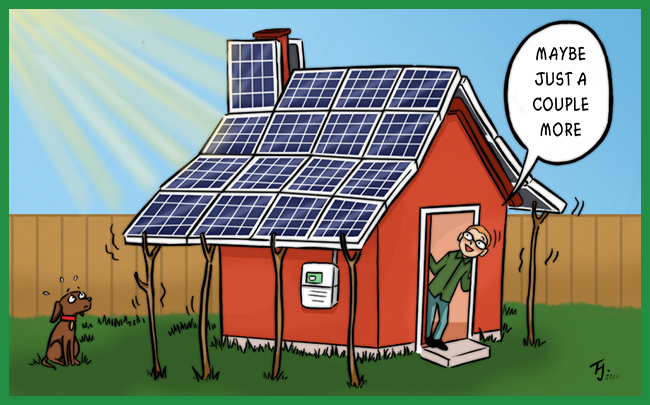
Let’s look at some of the runs?
The longest cable run row 1 is approximately 166 metres and we will assume that the Vmpp ( Voltage at Maximum Power Point) for this string is 800 volts.
The short circuit current of the panels in question are 10A so what is the volt drop using 4mm2 DC cable?
Voltage drop
Volt drop using 4mm2 over 166 metres
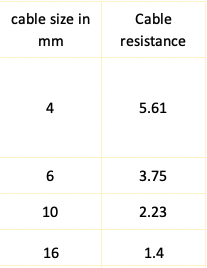
Using cable resistance Rc values from Table 35 in AS/NZS 3008
There is a total Vdrop of 18.63
As a percentage this 2.33%
So worst case scenario 4 mm2 cable is OK
If we used 6 mm2 the Vdrop is 1.56%
Calculation is (10A x 166L metres x 2 x 3.75R)/1000 then convert to a percentage by dividing into the 800 Vmpp
Which are we to choose?
https://www.jcalc.net/voltage-drop-calculator-as3008
Is 4 mm2 cable really OK for this run?
- The % Vdrop is under 3% but
- It’s pretty close!
- And what if we take into account an extra, say 5% - 10% margin?
- All questions to ask!
Using 4mm2 cable we have:
- 160 cable runs
- From each string to inverter station
- As we are not paralleling any strings this means 160 DC switches*
*we are assuming inverters have their own built in DC isolators
Double the current?
What if we decide to parallel the strings?
- We look at paralleling 2 x strings together
- We do this at the centre of each row
- We now have 80 cable runs to the inverter station
- At double the current, 20A
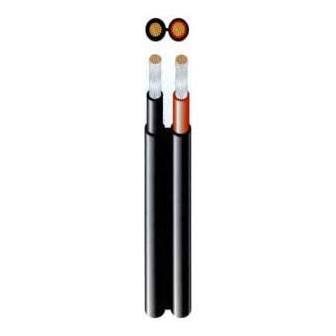
What cable satisfies our Volt drop requirements?
- Let’s look at 6 mm2
- longest run which is now 133 metres
- Volt drop % is 2.49%
But we have to add the cable run to the centre of the row!
Let’s say we use 4 mm2 for this 31 - 32 metre approximate run and we are carrying a current of only 10A and the Volt drop % is 0.43%
The sum of both volt drops is precariously close to 3%.
Probably best to use 6 mm2 also on this run @ 0.29%.
More things to consider
With a design that does not parallel can only use a minimum 4 mm2 but if we parallel, the minimum we can use is 6 mm2 on the longest runs.
Paralleling 2 x strings saves on the number of DC isolators used and it also saves on labour time, cables, less connections, less work.
From a cost perspective our design could use both 4 and 6 mm2!
Results
- Cable cost for 4 mm2 cable design is: 27,000 x $1 = $27,000
- Cable cost for 6 mm2 cable design is: 16,000 x $1.50= $24,000
- A difference of $3,000 on the cabling
6 mm2 is the winner based on this approach
But this is not the full story!!
Conclusion
- To parallel or not to parallel, that is the question
- All cable runs must take into consideration voltage drop requirements
- Materials and the labour component both must be taken into consideration
In part 3 we go into more detail.
Large solar projects, both ground mount and roof mount require a considerable amount of DC cable so there is definitely a need for a process and procedure that allows accurate calculations of these runs.
This is part two of a three part series.
If you’d like to see more of what Greenwood Solutions get up to in the real world of renewable energy, solar, battery storage and grid protection check out the following pages:
https://www.greenwoodsolutions.com.au/industry
https://www.greenwoodsolutions.com.au/commercial
https://www.greenwoodsolutions.com.au/commercial/customer-stories
https://www.greenwoodsolutions.com.au/news